Using ERP to Build Retail Supply Chain Resilience
The retail sector has undergone significant changes in recent years. Reshaped by the COVID-19 pandemic and the skyrocketing of e-commerce (which has only continued to grow), the industry is more dependent on a globalised economy than ever.
In spite of innovations that appear to break down barriers between producers and consumers, strong performance and profits can still be undercut by fragmented supply chains and other disruptions.
A 2022 report from McKinsey advised that these upheavals can be managed but only through proactive, long-term strategies for business resilience. A range of industries have made use of Enterprise Resource Planning systems to gain greater flexibility and bounce back from challenges presented by global economic uncertainty. Here we explore how retailers can leverage this technology to build more resilient supply chains.
What is supply chain resilience?
Supply chains regularly deal with disruption, and this has certainly been the global case in recent years. Covid-19, ongoing challenges arising from Brexit, and other geo-political and macro-economic crises have challenged business of all sizes, at every turn. Operational interruptions are not exclusively global either, and can come in many forms, such as unexpected developments in market trends, changes in consumer behaviour, new digital-first challengers winning business from established organisations, and other unforeseen developments.
A resilient supply chain is one with the agility and capacity to not only withstand and recover from these disruptions but to view them as opportunities. Through the use of technology and other resources to optimise supply chain strategies, businesses can upscale their processes, plan, forecast, and anticipate further disruptions, future proofing their operations for the long-term.
What are common retail supply chain issues?
Fluctuating demand
Change is the only constant in retail. Seasonal shifts in demand are nothing new, which makes them easier to plan for, but retail businesses often face unexpected surges in demand that require agile supply chain management. Selling online and in-store can present systemic challenges when delivering on a rapidly growing customer demand, alongside labour costs and issues.
Inventory management
Apparel businesses, for example, tend to operate with limited stock accuracy. To ensure order fulfilment is successful, inventory levels need to be transparent. When retailers do not know the quantities of stock they have on hand and its locations, this creates inefficiencies within supply chains—such as selling products that are not in stock.
Tight margins
Retailers have historically had low profit margins, but supply chain inefficiencies only serve to erode these margins further. Incorrect stock counts, out of stock items, and delivery delays all contribute to higher customer churn rate and, in turn, eat into retailer’s profits.
Omnichannel issues
The transition to e-commerce from traditional brick and mortar shops has changed the order fulfilment process and supply chain operations alongside it. Consumer expectations for a digital retail experience include online ordering, in-store pickup, free returns—all elements that make it harder for retailers to keep track of different channels.
Warehouse capacity
Last-mile logistics has become a key area of focus for many different industries in recent years, in part due to the impact of e-commerce and direct-to-consumer supply chains. Severe weather, seasonal fluctuations and difficulty predicting demand are just some factors that frequently lead to dwindling warehouse capacity and the rising costs of storage.
What is ERP?
Enterprise Resource Planning (ERP) systems give organisations full visibility over operations at any given time. They are designed to help with problem solving on the ground, and to enhance planning to improve efficiency.
ERP systems integrate and automate business processes like supply chains. They provide visibility into inefficiencies while enhancing the accuracy of communication between people and technologies, both internally and externally. ERP systems also have analytics capabilities that can collect, store, and interpret data for the purpose of optimisation.
In the retail sector, ERP makes it easier for businesses to carry out operations and collaborate with partners and supply chains, in order to build circular and more sustainable operations.
With Microsoft Dynamics 365 Business Central, an all-in-one ERP, you can connect your sales, service, finance and operations all within one single cloud-based application to achieve operational excellence by automating and streamlining your business processes.
And with a new-era of AI powered experiences and opportunities available through Microsoft Copilot in Dynamics 365 Business Central, organisations can adapt faster, innovate at scale, and enhance performance to ensure supply chain disruption is kept to a minimum.
Building a resilient supply chain with ERP
ERP systems, such as Microsoft Dynamics 365 Business Central, provide businesses with dashboards and reports that lets them monitor key performance indicators and supply chain metrics. They are hence already used to support a variety of supply chain management functions in retail (e.g. the fashion industry) and other sectors—including planning, procurement, inventory management, and other aspects of order fulfilment.
By enabling integration between retailer and supplier systems, eliminating error-prone interfaces and boosting efficiency, ERP systems may be the key for all retailers to build processes that can withstand disruptions and become more future proof.
Here are the key areas where ERP can elevate business’s performance in the face of disruption, and enable greater resilience:
Forecasting & planning
To better prepare for fluctuating customer demand, retail brands can use ERP to make more informed decisions and predictions to increase supply chain efficiency. ERP systems use a combination of historical demand, sales forecasts, and seasonal variation data to predict inventory needs. They also calculate a projected figure of future orders, accounting for market trends, seasonality, and geography.
The software schedules manufacturing to meet the volume of customer orders and ensures labour, machinery, and materials are available to keep production running smoothly and on schedule.
This is already evident in demand forecasting for fashion brands: when procuring inventory for the upcoming season, businesses can use real-time data insights from ERP system to make more fluid forecasts by comparing with pre-season plans, accounting for changes in actual sales, customer behaviour, and market information.
Inventory management
Inventory management systems have been adopted by many companies to help ensure they are sufficiently stocked and can complete orders with ease. ERP systems monitor inventory levels and automatically remind those in charge of stock orders when they need to reorder, using seasonal sales data, predicted customer demand, and lead times on their supplier’s end.
Advanced reporting from ERP lets businesses identify top-performing stock keeping units (SKUs), sales by location and the landed cost of goods sold (COGS). ERP systems also provide greater transparency and accuracy for existing inventory, with analytics functions that can be used for quality control, COGS, turnover rates and inventory shrinkage.
Real-time visibility
ERP software sheds light on complex and opaque production processes. For example, Copilot next-gen AI enhances visibility across distribution systems. With this, retail staff can better coordinate inventory, resourcing, and logistics to maintain on-time completion and delivery. In the event of unexpected disruption, having end-to-end visibility over all stages of production (plus real-time data sharing) gives businesses the power to quickly respond.
For example: real-time visibility allows for the early detection of a weather event or force majeure event that has the power to suddenly disrupt transportation routes needed for the delivery of consumer goods. This increases the lead time a business has to put resilience plans into action
Enhanced communications
ERP systems enhance communication and collaboration within businesses and with external suppliers. The ERP dashboard or portal gives suppliers and customers a line of communication with the business to track orders.
This helps make business-as-usual as seamless as possible, but in times of unexpected disruption, it is especially helpful for enabling all stakeholders to align and make quick decisions. When all data is centralised, the internal barriers and siloes between different departments are broken down with all relevant information available to everyone in an organisation.
Digital transformation for supply chain resilience
Retailers continue to face challenges in an increasingly complex commercial landscape, before even accounting for supply chain shocks. With the right systems and approach, organisations can become agile enough to not only weather storms, but embrace them with a disruptive mindset.
Xpedition collaborates with your team to digitally transform your existing systems and drive efficiency. Supported by Microsoft Dynamics 365 Business Central and K3 Pebblestone, our solutions harness an innovative approach and are developed to make operations decisions faster, easier and make businesses more competitive.
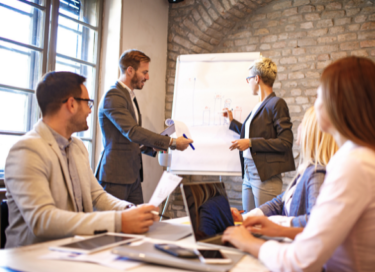
7 Lessons Learned in the jump from Dynamics NAV to Business Central
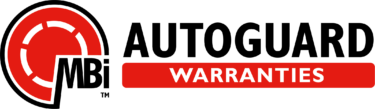
Autoguard Group streamlines finance operations with Microsoft Dynamics 365 Business Central
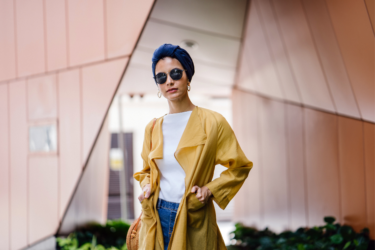
7 Ways to Achieve Sustainability in Fashion
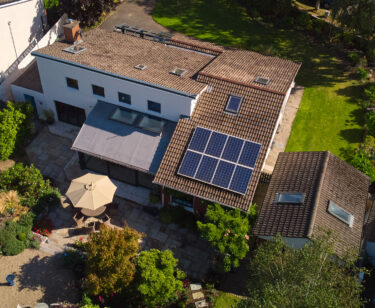